Dremeling out holes for knobs, switches and displays is fun, but several companies now offer cheap laser cutting that lets you make a custom acrylic box with all the right holes and dimensions for under $30. This post talks about how to draw the 6 sides using free software, and how to connect the pieces using screw-together and permanent techniques.
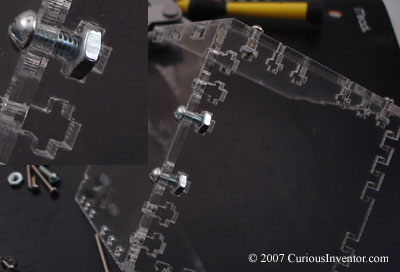
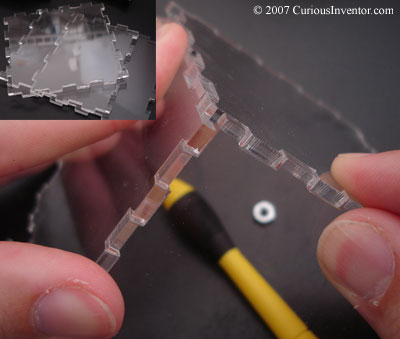
Making decent enclosures is troublesome because it’s almost impossible to find just the right size box, and hacking out the holes for connectors usually takes a lot of time and looks sloppy at best. Designing your own laser-cut, acrylic box takes care of these issues and doesn’t even cost that much.
Ohararp.com got our pieces to us in 3 days and cost less than $30.
Pololu also does cheap cutting.
This will go over our experimentation with a couple different joint styles, some chemically welded with acetone and others held together with screws and nuts. We’ll also talk about drawing the sides with free software and stress test the results.
Joing Two Pieces of Acrylic:
Permanent Joints: If you want a permanent joint, there are lots of guides already out there that demonstrate using made-for-aquarium glues and / or acetone. We put together two corners using plain acetone: one with flat edges and one with a puzzle-like square wave pattern to see if that added strength. Result: the flat edged (green) corner came apart with a light tug. The puzzle-piece corner (clear) has yet to be destroyed, despite trying to tear it apart at near full-strength. Interestingly, both were water-tight. Instructions for chemically welding with acetone are below.
Temporary Joints: You typically want to be able to open your box to fix circuitry, replace batteries, etc., so gluing everything together won’t work all the time.
The sturdiest route would probably be to use metal, threaded-inserts that you install by first pre-drilling a hole into the edge, and then “heat staking,” or melting the insert into the plastic (using a soldering iron). You can actually tap (cut screw threads) directly into acrylic, too.
Both of these technique require drilling into the side of the plastic, however, and we wanted something that could be completely cut out of a flat sheet with a laser. We also couldn’t find inserts that would fit in 1/8″ acrylic.
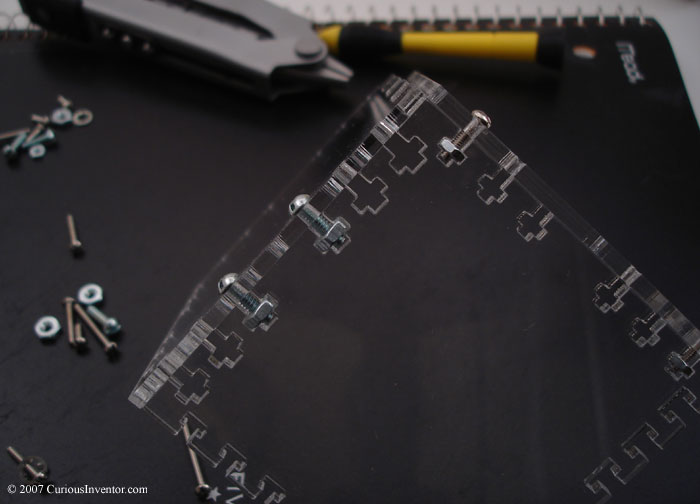
Another idea, used extensively by the
fabathome people, is to use “T”-nuts. A T-shaped gap is made in the edge so that a flat nut can be inserted from the side into the top of the T. Here’s a
picof one of the fab at home machines show casing this technique. Unfortunately, we couldn’t find T-nuts small enough, so we decided to try the same idea using just regular nuts. By the way, a lot of these ideas were dreamed up by Daved @
uCHobby.com.
Designing the Joints:
With either the screw-together or glue-together technique, we weren’t sure if the laser would leave a gap for which we’d have to account. As it turns out, at least with ohararp, what little gap there is appears to be under a thousandth of an inch (as measured with calipers). This means that we didn’t have to design in extra material for the width of the laser cut.
Screw Together Joints:
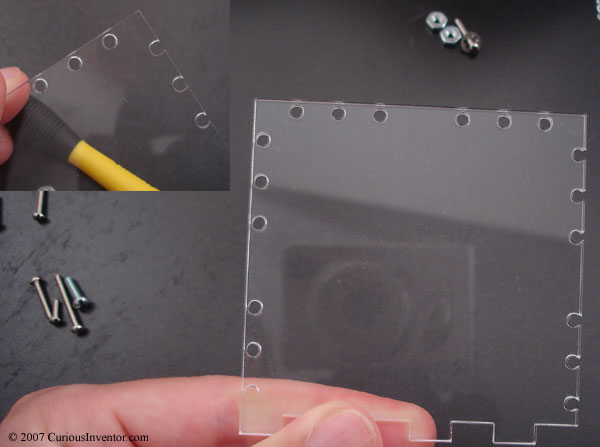
The above two pictures show several different sizes and spacings for the cuts. Although they look the same, each T-cut is slightly different. We wanted to see how “extra space” would affect things. The joint seemed to work just as well regardless of whether the T-cut was exactly the same as the nut or a few thousandths larger.
Both 2-56 and 4-40 screws and nuts were used. In all cases, the nuts stick out, but the acrylic sides can be designed to be flush (not overhang) by placing the center of the holes 1/2 the material thickness from the edge. As the picture shows, placing the holes that close to the edge caused the 4-40 screw holes to be interrupted by the outer edge, but the joint seemed to work just as well. Exact dimensions will be shown in the next section.
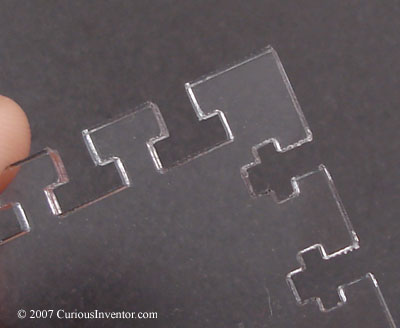
One useful trick was to make a lower-case t-shape to allow the screw to extend past the nut. This avoids having to use screws that are exactly the right length.
Glue / Chemically Welded Joints
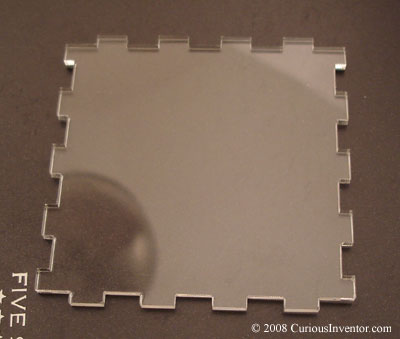
We tried both a flat edge version and checkered edge (shown above) to see if the puzzle-piece connection added much strength.
There’s actually software out there that will automatically generate dwg/dxf files given arbitrary box dimensions called
Box Maker. This is great if you don’t need to cut your own holes for display and switches, etc.
Drawing the Box Sides with Free Software:
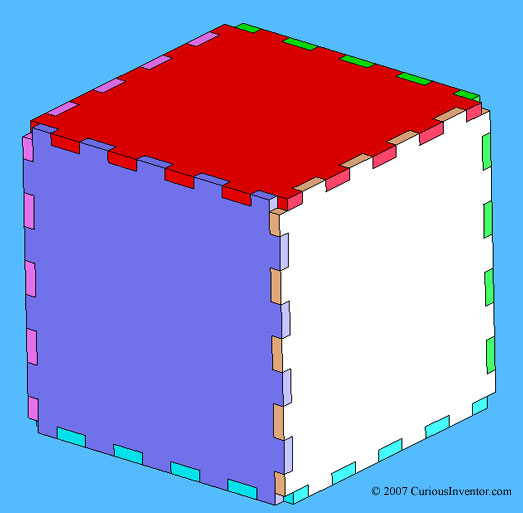
First some pseudo-code for making the square-wave pattern. The above cube is made of 6 copies of the following panel.

First draw the outline of one face, then sub-divide it into 9 columns and rows, the odd number being important. Then use an offset tool to draw another set of lines inside the outer box by the thickness of the material.
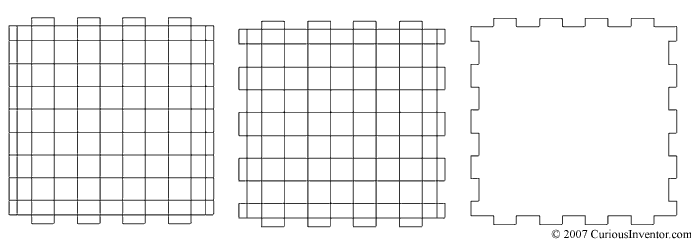
Now get out the trim tool. Two opposite sides should have high portions of the square wave at the edge, and the other two should form the inverse. 4 of the tabs will be a little thinner than the others to allow 3 pieces to fit together at the corners.
Drawing the T-shaped holes
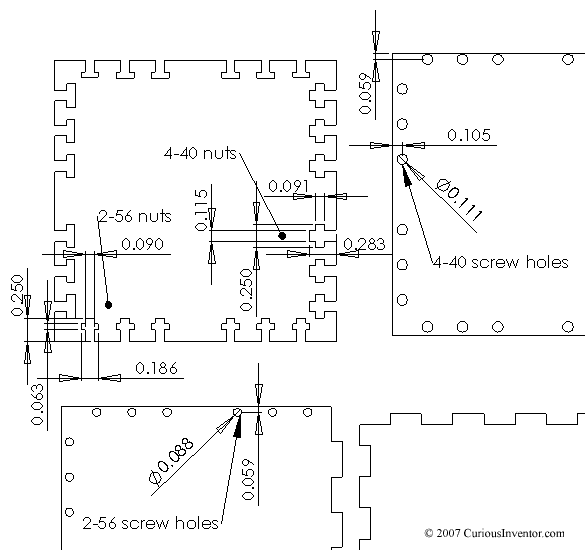
The dimensions on the t-shaped holes were barely big enough for the nuts, but we found the joints still worked well with a little extra slop. Not all nuts are created equal, you might want to add in a couple thousandths margin.
If you don’t want any overhang, draw the clearance holes for the screws at half the thickness of the material. This will cause a 4-40 hole to go past the edge on .118″ thick material, but this didn’t seem to hurt the joint much. Compression holds the pieces together, not the side wall of the screw hole.
Free CAD Software:
Talk to your laser cutter to see what format they will accept. Typically, any sort of vector-based file will work, such as dxf or eps will work.
- Alibre: From our very brief testing, this appears to be one of the best free offerings out there. 2D and 3D, similar feel to SolidWorks if you’re used to that.
- freebyte.com/cad: A good listing of free / open source software.
- Cademia: open source and cross platform
- QCad: Only free for linux.
- SolidEdge: 2D only, fairly easy to use interface.
- A9Tech: The simplest to use out of the box, you can save as dxf, but not pdf, jpg, etc.
- CADStd: Another fairly easy-to-use windows program that exports dxf.
- Many drawing programs will also work, and if you already have a CAD program (like Eagle) for electric circuits, check to see if it will export dxf.
Be prepared to fight a learning curve if you’ve never used a CAD program before; they’re a little trickier than photoshop. Some tools to get familiar with include O-snaps, linear patterns and offsets.
Welding the Acrylic Sides Together with Acetone
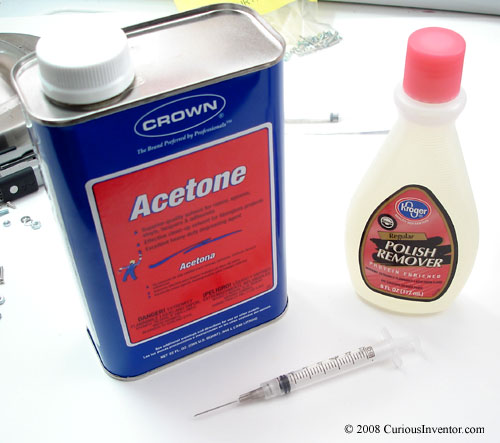
Lots of guides recommend using a special aquarium glue to join pieces together, but we had success just using straight acetone from the hardware store. This may only work well when the gaps are very small and capillary action can pull the acetone between them.
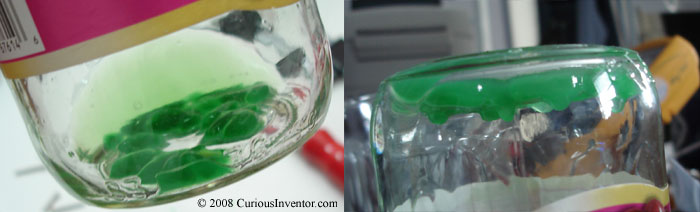
If there are rougher edges, some recommend making a mixture of acetone and acrylic by dissolving some acrylic pieces in a jar of acetone over night. The thicker mix may better fill gaps. After a few hours, the acrylic starts to soften (left), and after a day, a thick syrup is all that remains.
The syringe is very helpful for applying the acetone only to the joint. Any spills will immediately start eating into the plastic and damaging the surface. I got a free one from a local Kroger pharmacy. I think the pharmacist actually believed me when I said it was for a hobby project.
About Acetone: Acetone is an interesting chemical, commonly used to thin epoxies, remove paint, clean greased parts (bicycles), it is also the main ingredient in nail polish remover. (We tried using nail polish remover to join parts, it did not work…)
deoxy.org says even the vapors can damage cds. It evaporates quickly, is highly flammable, and is heavier that air, so it’s probably not a good idea to use near a pilot light. The fumes attack the central nervous system (see msds), can harm the lungs, and eventually cause unconsciousness. The liquid will damage skin.
It also makes great acrylic joints!
According to
wiki/Plastic Welding, in solvent welding, acetone dissolves the plastic which allows the sides to “mix”. Then it eventually permeates out leaving behind a solid acrylic connection.
Clamp or Tape the Pieces Together:
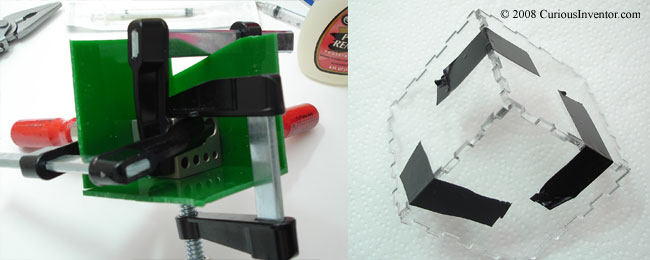
First, figure out a way to clamp or tape the pieces together. The green pieces have straight edges and the clear ones have square-wave shaped edges that fit together like a puzzle. Clamping the pieces (green) to a block turned out to be a bad idea because the acetone was pulled underneath it.
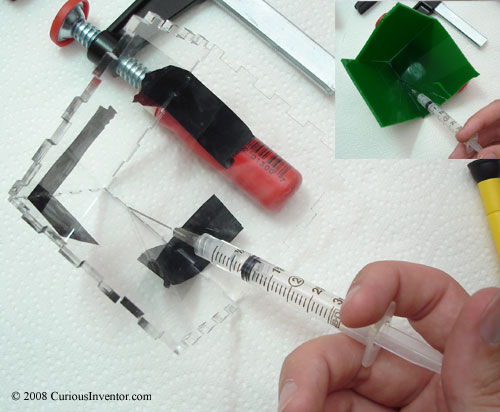
Now apply a small amount of acetone with the syringe along the inside seam. Capillary action should pull it into the joint. We repeated this a few times to make sure all the gaps were filled, letting it sit a few minutes between each application.
Let it sit for 24 hours. It might be fine after 2 or 4 hours, test for yourself!
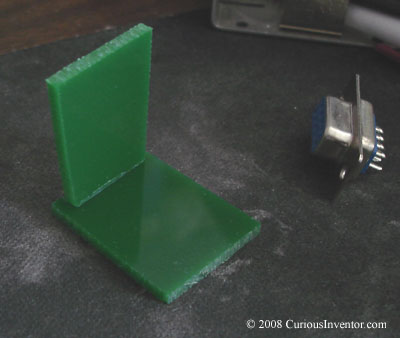
To get a better idea on the strength of a straight edge joint, we made a small 1″ joint, also. Surprisingly, it survived over 3 lbs of tensile force before breaking!
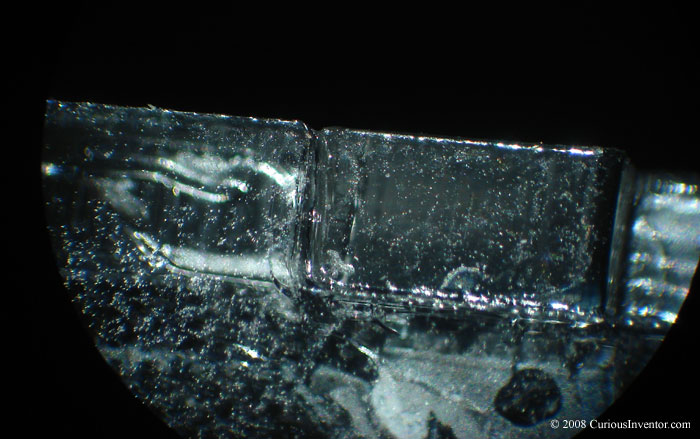
Wonder whether the gaps actually got filled? Here’s a picture under 20X magnification after everything has hardened. Almost every single gap was completely filled.
Conclusions:
Acetone Welded Pieces: As we mentioned at the beginning, the square-wave puzzle-shaped edge was amazingly strong, whereas the flat edges broke easily. This could have been due to some unevenness in the flat edge, since the small 1″ test piece survived over 3 lbs of force over a very small area. One thing to watch out for is the acetone being wicked away from the joint by whatever is clamping the pieces together. You can see some marks where it got under the tape in the final picture below.
T-Slot Screw-Together Method: These joints seemed surprisingly strong. Some lock washers would probably help prevent loosening from vibration. One downside is that the nuts stick out from the side a bit, but there might be some smaller t-nuts out there that will fit inside a 1/8″ or 3/16″ piece of acrylic. Another method might involve making tabs on one piece of acrylic that fit into slots on another, with everything being held together with long screws and standoffs. Leave better ideas and corrections in the comments… this isn’t a tried-and-true method yet!