Description
All taps are plug type, ground threads from HSS (High Speed Steel), and coarse threads. The H-Limits are as follows: 4-40:H2, 6-32:H3, 8-32:H3, 10-24:H3, 1/4-20:H5. Information at the end of this section describes different tap parameters. Instructions for use: For instructions on tapping along with other metal working basics, watch this video. A brief summary: First, use some sort of oil or cutting fluid, we recommend Tap Magic. While pressing down firmly, make 2-3 complete revolutions. After this, rotate forward a quarter revolution, and then backwards a half revolution to break off chips. If it gets stuck, back all the way out and clear out the chips, never force the tap. You may be able to reverse less often, but be careful. A broken tap can be almost impossible to remove, and usually cannot be drilled out because taps are harder than most drill bits. The most critical part is starting straight. The following picture illustrates the use of a tapping block–a block of metal with holes slightly larger than the tap. This wrench has a hole on its top that can be used as a guide in a drill press by pressing down gently on the quill (2nd pic).
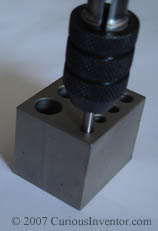
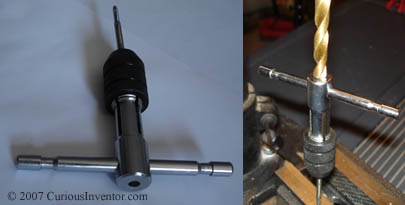
A little about the different varieties of taps: We’ve selected the most commonly needed tap for hobbyists and general work needs, but there are situations when you’ll need something different. The following list describes the main parameters to decide between when choosing a tap:
- Coarse or Fine threads: Coarse threads are stronger, faster to install, much more common, less likely to jam, and less sensitive to dirt or damage. Fine threads have more threads per inch, and are usually only used when tapping thin material, like sheet metal.
- Ground or cut threads: Ground threads are more precise than cut threads, but slightly more expensive.
- Plug / Bottoming / Taper: This refers to the chamfer on the front of the tap. Plug is most common and has a chamfer on the first 3-5 threads. Taper taps have a chamfer on the first 8 or more threads, and bottoming taps have less than 3 threads tapered. Taper taps are sometimes used on extremely hard materials because the cutting action is spread over more threads. Bottoming taps are used when threads must go all the way to the end of a blind hole (dead end hole). A plug tap is first used as far as possible, and then a bottoming tap finishes the hole.
- H or High Limit: This refers to how over-sized the tap is. Taps are manufactured over-sized so that they can wear down slightly and still create threads within spec. Of coarse, it can’t be too over-sized because the tap would create threads too large. Typical advice is to select the largest H value that still falls within specified limits, so that the tap lasts as long as possible. This is slightly tricky because taps cut somewhat larger than their true size.
- Number of flutes: In general, more flutes increase the strength of the tap, but limit space for chips.
- Gun and other taps: There are a variety of other tap styles that can be used in machine operation. Gun taps, for instance, push chips in front of them, and therefore don’t need to be reversed.
- Surface finish and material: HSS is sufficient for most purposes, but TiN (Titanium Nitride) coatings and different tap materials like cobalt, or carbide edges will last longer and withstand tougher materials.
Reviews
There are no reviews yet.